Morteros autonivelantes
Industrial

Especial para nivelación, alisado y reforma de pavimentos industriales con tráfico moderado o pesado.
Su espesor está comprendido entre 5 y 30 mm con una composición de ligantes hidráulicos, resinas poliméricas, fibra de vidrio, áridos y aditivos.
El mortero industrial proporciona al pavimento, las prestaciones técnicas necesarias para tener una alta firmeza al desgaste.
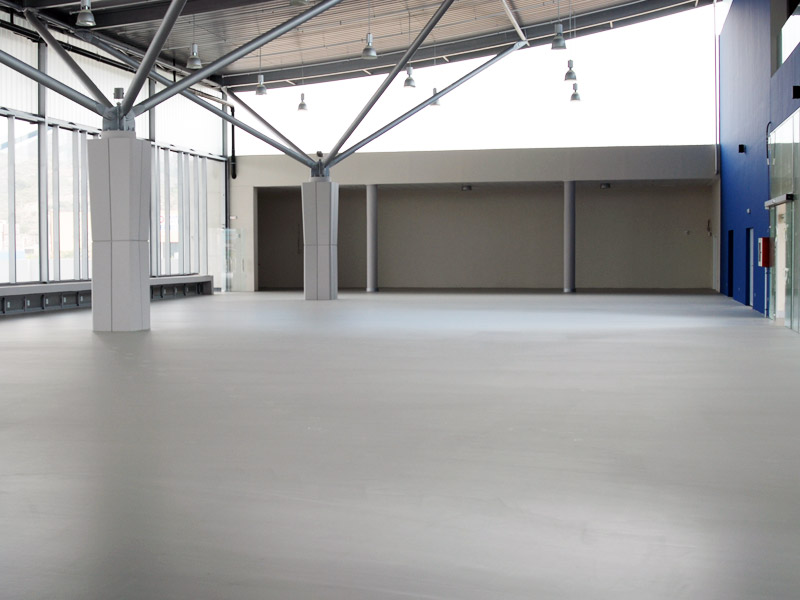
Más Información
Ficha Técnica
DESCRIPCIÓN DEL PRODUCTO
El Autonivelante Industrial es un mortero auto nivelante bombeable, de fraguado rápido, basado en cemento y modificado por polímeros, con alta resistencia al desgaste para su uso en industrias con tráfico moderado e intenso. El grosor de capa está entre 5 y 30 mm.
De acuerdo con la norma EN 13813 para suelos sometidos a estrés mecánico intenso en instalaciones industriales el Autonivelante Industrial está clasificado como CT-C30-F7 y resistencia a la abrasión RWA1, según la norma UNE-EN 13813, Anexo ZA1.1.
PROPIEDADES
- Espesores entre 5 y 30 mm.
- Gran poder de nivelación.
- Endurecimiento rápido y rápida puesta en servicio.
- Capacidad autoportante (mínimo 25 mm).
- Armado con fibra de vidrio.
- Gran durabilidad, sometido a cargas mecánicas elevadas.
- Alta resistencia al desgaste por abrasión.
- Bombeable.
- Retracción compensada.
- Tiempo de revestimiento:
- Alicatado, moqueta: 8 a 12 horas.
- Parquet, plásticos: 12 a 24 horas.
- Resinas: 48 horas (invierno) – 24 horas (verano).
USO RECOMENDADO
EL Autonivelante Industrial ha sido diseñado para emplearse en entornos industriales, tanto en suelos nuevos como en proyectos de renovación. Se emplea para el nivelado y el alisado de suelos sometidos a condiciones de tráfico intenso y abrasión, en instalaciones como fábricas, áreas de producción y almacenes. Especialmente indicado para la renovación de garajes, industria y la reparación de sustratos en mal estado. Altamente indicado para ser revestido con pinturas epoxi, poliuretanos, linóleos, PVC, moquetas, parquet, etc. Este producto debe ser utilizado exclusivamente en interiores.
CARACTERISTICAS TÉCNICAS
Presentación: | Polvo cementoso. |
Espesor: | De 5 mm a 30 mm. |
Solubilidad: | Parcialmente soluble en agua. |
Tiempo de secado a 20 ºC y 65% H.R | Para tráfico peatonal: 2 a 4 horas.
Para tráfico ligero: Transcurridas 24 horas. Para tráfico normal: Transcurridos 7 días. |
Tiempo de secado antes de revestir: | Alicatado, moqueta: 8 a 12 h.
Parquet, plásticos: 12 a 24 h. Resinas: 24 h en verano y 48 en invierno. |
Tiempo de trabajo: | Aproximadamente de 15 a 20 minutos a 20ºC. Puede variar con los factores ambientales de temperatura y humedad relativa. |
Olor: | Ligero olor |
Vida útil: | 9 meses a partir de la fecha de fabricación, en envase original cerrado y al abrigo de la humedad. |
Almacenamiento: | Conservar bajo techo a temperaturas entre 10ºC y 35ºC.
Almacenar el embase, bien cerrado y separado del piso en lugar seco y fresco. |
Envases: | Sacos de 25 kg. |
Resistencia de adherencia del sustrato | >1,0 MPa (N/mm2). |
Resistencia a la compresión transcurridos 28 días: | C30, 32 MPa (N/mm2) EN 13892-2. |
Clasificación resistencia flexión transcurridos 28 días: | F7, 5 MPa (N/mm2) EN 13892-2. |
Retracción transcurridos 28 días: | < 0,4 mm/m EN 13454-2. |
Reacción al fuego: | A1fl, EN 13501-1. |
Resistencia al deslizamiento: | Clase 2. |
PREPARACIÓN DE LA BASE Y APLICACIÓN DEL PRODUCTO
Útiles: Llana dentada, bomba mezcladora, rodillo de púas.
Rendimiento: Aproximadamente 1,70 kg/mm/m2.
Preparación de la base:
- El substrato deberá estar asentado, seco, libre de polvo, grasa y demás impurezas que pudieran dificultar la adhesión.
- Si es necesario, el substrato deberá ser tratado mecánicamente mediante abrasión mecánica o granallado.
- Los agujeros y poros que el substrato pudiera presentar deberán ser adecuadamente sellados.
- Las tomas eléctricas, y demás elementos, deberán ser protegidos con tapas y separados mediante limitadores.
- Los soportes porosos como mortero u hormigón se deben aplicar imprimaciones poliméricas o mediante puente de adherencia, Es recomendable imprimar en dos capas.
- Sobre soportes no porosos (cerámica), realizar una limpieza por abrasión mecánica e imprimar la superficie con el puente de adherencia epoxídico saturado con árido.
Preparación del producto:
- Realizar una mezcla entre el componente polvo con agua limpia mediante batidor eléctrico o máquina de bombear en una proporción de 5,25 litros por saco de 25 kg.
- Si es manualmente se debe añadir al recipiente en primer lugar el líquido y luego poco a poco ir vertiendo el polvo, sin dejar de mezclar con la hélice hasta que se haga una mezcla homogénea.
- Si es mediante bombeo las propiedades de fluidez del producto deberán ser comprobadas mediante un ensayo de fluidez (245-250 mm de diámetro/cono estándar) antes y durante el bombeo, empleando un anillo medidor de flujo y una placa.
- Un exceso de agua causa la separación y debilita la resistencia de la superficie del mortero. Por ello, no añada una cantidad excesiva de agua a la masa.
Aplicación:
- El mortero debe ser bombeado o vaciado sobre el substrato en secciones. Cada nueva sección debe ser aplicada sobre la anterior tan rápidamente como sea posible. La anchura máxima del área de bombeo varía entre 6 y 8 metros, dependiendo de la capacidad de la bomba mezcladora y del grosor de capa que se requiera. Las áreas de mayor extensión pueden ser temporalmente divididas mediante delimitadores. Trace siempre una línea recta antes de pegar el delimitador al substrato.
- Inmediatamente después del bombeo y con la ayuda de una llana dentada, podrá facilitar el proceso de autonivelación del mortero y eliminar de la superficie las burbujas y estelas producidas por el movimiento de la manguera. Posteriormente, podremos usar un rodillo de púas (longitud de la púa 20-30 mm), para eliminar el posible aire ocluido en el mortero.
Limpieza de utensilios: Las herramientas se pueden limpiar con agua inmediatamente después de su uso. El material endurecido se tiene que retirar mecánicamente.
Tratamientos posteriores:
- Las superficies de aplicación que estén frescas deben ser protegidas de las corrientes de aire, de la radiación solar directa y del calor excesivo. Durante la aplicación y durante la semana posterior a ésta, la temperatura del interior deberá ser superior a 10ºC.
- Realizar un lijado superficial y aspirado previo a la aplicación del revestimiento final (como de resinas epoxi, poliuretanos, linóleos, PVC, etc.).
Observaciones:
- Siempre se deberá usar junta perimetral y es recomendable cortar las juntas estructurales del hormigón. En caso de duda relativa a la aplicación, el substrato o las características constructivas del producto, consulte con el técnico especializado.
- El producto se endurece tras la mezcla con agua, y puede ser desechado como residuo de construcción, de la misma manera que los morteros minerales
EQUIPO DE PROTECCIÓN PERSONAL Y PRECAUCIONES
- Guantes de protección adecuados y resistentes.
- Botas de seguridad para la manipulación y aplicación del producto.
- Rodilleras para la aplicación en suelos o superficies donde se apoyen las piernas.
- Gafas protectoras con protección lateral para el proceso de mezclado.
- Mascarilla para polvo en el proceso de lijado.
- Evitar el contacto prolongado con la piel.
- No ingerir
- Mantener fuera del alcance de los niños
- Este producto es de uso exclusivo de profesionales.
GARANTÍA DE CALIDAD
IngreMic S.L. asegura la calidad de su producto incluyendo el cuidado y embellecimiento, siempre que se respeten y sigan las instrucciones especificadas en esta ficha técnica.
Estas instrucciones corresponden al estado actual de nuestros conocimientos y facilitan información general acerca de la aplicación y características de nuestro producto.
Se recomienda la realización de visitas técnicas antes de iniciar un trabajo para ver el estado de las bases y la viabilidad del proyecto. En los casos de dudas consultar a nuestro servicio técnico.
Ficha de Seguridad
FICHA DE SEGURIDAD
Conforme al Real Decreto de 255/2003 de 28 de febrero. (B.O.E. 4-3-2003)
Revisión: Nº 2, FEBRERO/2004
1. – Producto
Designación certificada en el mercado | Designación según
UNE-EN 197-1 |
Cemento Portland, con caliza, CEM II / A- LL 32.5 N | CEM II / A – LL |
Cemento Portland Blanco BL II / A- LL 52.5 R | CEM II / A- LL |
1.2 Uso del producto: Fabricación de microcemento
1.3 Identificación de la empresa: IngreMic S.L.
Carretera de Barcelona 278 ,Local 08210 Barberá del Valles Teléfono: 913779200
1.4 Contacto: 931817228 Showroom IngreMic
Emergencias: 915 62 04 20 INSTITUTO NACIONAL DE TOXICOLOGIA
2. – Composición del producto / características de los componentes:
El microcemento esta compuesto de cemento clínker y otros componentes en distintas proporciones en masa, según la siguiente tabla de la norma UNE-EN 197-1: 2000 |
||||||||||||||
Principales tipos |
Designación de los productos (tipos de microcementos comunes) |
Composición (proporción en masa (1)) | ||||||||||||
Componentes principales |
Constit. Minorit. |
|||||||||||||
Clinker
K |
Escoria de horno alto
S |
Humo de sílice
D 2) |
Puzolana |
Cenizas volantes |
Esquistos calcinados
T |
Caliza |
||||||||
Natural
P |
natural calcinada Q | silíceos
V |
calcicas
W |
L |
LL |
|||||||||
CEM II/A-LL | 80-94 | – | – | – | – | – | – | – | – | 6-20 | 0-5 | |||
CEM II/B-LL | 65-79 | – | – | – | – | – | – | – | – | 21-35 | 0-5 | |||
1) Los valores de la tabla se refieren a la suma de los componentes principales y minoritarios (núcleo de cemento).
2) El porcentaje de humo de sílice está limitado al 10%. 3) En cementos Portland compuestos CEM II/A-M y CEM II/B-M, en cementos puzolánicos CEM IV/A y CEM IV/B y en cementos compuestos CEM V/A y CEM V/B los componentes principales además del clinker deben ser declarados en la designación del cemento (véase apartado 8). |
||||||||||||||
y, además con la cantidad necesaria de sulfato de calcio, para regular el fraguado, de forma tal que el contenido de S03 en el cemento no exceda el 4.5% |
COMPOSICIÓN BL 22.5 X según UNE 80.305: 2001; como mínimo un 40% de Clinker cemento, un máximo de 1% de materias orgánicas, en su caso, y el resto de materiales inorgánicos.
Componentes:
- Clinker: EINECS 266-043-4 (NºC.A.S. 65997-15-1) esta compuesto principalmente de silicato, aluminato y ferritoaluminato de calcio, pequeñas cantidades de cal libre, oxido de magnesio, sulfato de sodio, potasio y calcio.
- Puzolana
- Cenizas volantes silíceas ( Nº C.A.S. 68131-74-8)
- Escoria siderúrgica (Nº C.A.S. 65996-69-2)
- Caliza
- Sulfato de calcio : en forma de yeso (NºC.A.S. 10101-41-4)
3.- Peligros Identificados
3.1. Clasificación del preparado
Irritante (Xi)
3.2. Principales peligros para la salud humana
Contacto cutáneo:
- Microcemento seco:
Puede provocar sequedad de la piel seguida de leve irritación
- Microcemento en contacto con piel húmeda o cemento mezclado con agua:
Puede provocar efectos cutáneos más severos como agrietamiento de la piel. Una exposición más prolongada puede ocasionar efectos más severos en forma de quemaduras cáusticas debido a su pH elevado
Contacto ocular:
- • Cemento seco en poca cantidad:
Puede causar una leve irritación en los ojos
- Cemento seco en gran cantidad o proyecciones de cemento mezclado con agua:
Pueden causar efectos que van desde una moderada irritación de los ojos hasta quemaduras cáusticas.
Inhalación:
La inhalación de polvo de cemento más allá de los límites de exposición ambiental permisibles puede provocar la irritación de las vías respiratorias
Ingestión:
La ingestión de este producto es poco probable a menos que se trate de un acto deliberado. Pequeñas ingestas de polvo no son dañinas pero en cantidades significativas, pueden ocasionar dolores abdominales y/o irritación del tracto digestivo.
3.3. Principales peligros para el medio ambiente
El microcemento no presenta riesgo particular para el medio ambiente, siempre que se respeten las recomendaciones de los puntos 7, 12 y 13.
4.- Primeros Auxilios
Inhalación
Si una persona presenta trastornos por la inhalación de grandes cantidades de microcemento, se le trasladará inmediatamente a un lugar al aire libre. En caso de paro respiratorio emplear el método de reanimación cardiopulmonar (RCP) Mantener al paciente abrigado y acostado. Conseguir atención médica tan pronto como sea posible.
Contacto cutáneo
Si el contacto con el polvo de microcemento o microcemento mezclado con agua produce irritaciones, lavar con agua abundante la parte afectada y si persiste la irritación consultar al médico.
Contacto ocular
Si el microcemento o el cemento mezclado con agua, entra en los ojos, evitar la compresión y la introducción de instrumentos para eliminarlo. Lavar los ojos con abundante cantidad de agua y solicitar asistencia médica.
No deben usarse lentes de contacto cuando se trabaje con este producto de no ser que se utilice una protección adecuada.
Ingestión
No inducir al vómito y procurar asistencia médica. Si la persona está consciente darle a beber gran cantidad de agua. Buscar inmediatamente ayuda médica.
5. – Medidas de lucha contra incendios:
El microcemento no es inflamable.
El microcemento, en caso de incendio, no limita el uso de agentes de extinción.
6. – Medidas en caso de vertido accidental
6.1. Precauciones personales: Evitar todo contacto con los ojos. Evitar el contacto con la piel. Evitar respirar el polvo. En caso de atmósfera de polvo de microcemento utilizar una mascarilla antipolvo homologada. Manipular el producto con guantes impermeables.
6.2. Precauciones para la protección del medio ambiente: No verter microcemento en alcantarillas y en las aguas superficiales.
6.3. Métodos de limpieza: No limpiar microcemento barriendo ni soplando, utilizar un método apropiado para evitar levantar polvo. Después de fraguado, el cemento puede ser evacuado como un residuo inerte. El cemento mezclado con agua tarda en endurecer entre 30 y 90 minutos.
7. – Manipulación y Almacenaje:
7.1. Manipulación
- El suministro de este material se realiza a granel en cubas que posteriormente se descargan en silos cerrados o bien en sacos de papel o big bags.
- Los silos para la descarga de las cubas deberán estar provistos de un sistema de filtración del aire de escape.
- En los locales donde se manipule el producto se deberá garantizar una buena ventilación.
- Evitar nubes de polvo durante la manipulación. Si no es así llevar gafas y mascarilla antipolvo homologadas.
- Evitar el contacto directo del cemento con la piel y las mucosas.
- Observar una higiene personal adecuada.
- No comer durante la manipulación del producto.
7.2. Almacenaje
- No es necesario tener ninguna precaución especial en el almacenamiento salvo el proteger los sacos de papel de la humedad para evitar su rotura y los consiguientes derrames del producto.
- Mantener fuera del alcance de los niños.
8. – Controles de la exposición:
8.1. Valores límites de la exposición
Los límites de exposición profesional actual para el cemento vienen dados por los Valores Límites Ambientales de Exposición Diaria según R.D. 374/2001, de 6 de abril : VLA/ED (8 horas) = 10 mg/m3.
8.2. Controles de la exposición profesional
Protección respiratoria: En caso de presencia de polvo de cemento en el aire usar mascarilla específica para partículas.
Protección cutánea: Llevar guantes impermeables, para su uso en mezclas acuosas. Llevar la indumentaria adecuada adaptada al tipo de trabajo y proteger la piel de proyecciones de pasta de cemento húmeda. Cuando se tenga que trabajar arrodillado se recomienda rodilleras impermeables.
Protección de los ojos: Llevar gafas de protección homologadas en caso de riesgo de polvo o de proyección de pasta sobre los ojos.
9. – Propiedades Físicas y Químicas:
Información general:
- Aspecto: Polvo gris ó blanco.
- Olor: Inodoro
Información importante en relación con la salud, la seguridad y el medio ambiente:
- pH en solución acuosa: básico entre 11 y 13.5
- Temperatura de fusión: >1000ºC
- Densidad absoluta: de 2.8 a 3.2 g/cm 3 a 20 ºC
- Densidad aparente: de 0.9 a 1,2 g/cm3 a 20ºC
- Solubilidad en agua: 1.5 g/l a 20 ºC
- Temperatura de inflamación: No aplicable
- Granulometría: del orden de 20 a 30% de finos < 5 micras.
10. – Estabilidad y reactividad:
Estabilidad: El producto es estable
Condiciones que deben evitarse: La humedad puede provocar el fraguado del cemento.
Materias que deben evitarse: Ninguna
Productos de descomposición peligrosos: Ninguno
11. – Información toxicológica:
Inhalación:
El cemento puede provocar irritación de las vías respiratorias.
El cemento puede provocar irritación de la mucosa nasal. En casos extremos se ha observado una erosión de la mucosa.
Ingestión:
En caso de ingestión significativa, el cemento puede causar la irritación del tracto digestivo y provocar dolores abdominales
Contacto con la piel:
El cemento puede irritar la piel por tener sus soluciones acuosas un pH elevado e incluso puede llegar a provocar quemaduras cáusticas en exposiciones significativas.
Contacto con los ojos:
Si entra cemento en los ojos puede producir conjuntivitis, irritación de los párpados (blefaritis) y provocar lesiones de los globos oculares.
Patología crónica cutánea:
En caso de contacto prolongado sin protección, pueden aparecer lesiones como dermatitis fisurativas, ulceraciones, hiperqueratosis, generalmente en los dedos.
12. – Información ecológica.
Ecotoxicidad: En caso de derrame accidental de cemento en el agua se puede producir una débil subida de su pH . El cemento fraguado es un material estable que fija sus compuestos y los hace insolubles.
Movilidad: Ninguna.
Persistencia y degradabilidad: Ninguna.
Potencial de bioacumulación: Ninguno.
Otros efectos nocivos: Ninguno.
13. – Consideraciones relativas a la eliminación:
El microcemento puede ser eliminado como otros residuos de construcción y almacenado respetando la reglamentación en vigor.
14. – Información relativa al transporte:
Mercancía no peligrosa según la reglamentación de transporte.
15. – Información reglamentaria
Símbolo de peligro: Xi (irritante)
Componentes principales: cemento.
Frases R:
R36/37/38: Irrita los ojos, las vías respiratorias y la piel.
Frases S:
S2: Manténgase fuera del alcance de los niños.
S 24/25: Evítese el contacto con los ojos y la piel.
S26: En caso de contacto con los ojos, lávense inmediata y abundantemente con agua y acúdase a un medico.
S37/39: Úsense guantes adecuados y protección de para los ojos/ la cara.
16. – Otra información:
Es responsabilidad del usuario tomar las medidas de protección adecuadas.
La información suministrada en esta ficha se da de acuerdo con los datos disponibles a la fecha de la revisión de la misma.
Garantía del producto
IngreMic asegura la calidad de sus productos incluyendo el cuidado y embellecimiento, siempre que se respeten y sigan las instrucciones especificadas en las correspondientes fichas técnicas. A su vez certificamos la excelente calidad que posee la materia prima utilizada y todos sus componentes.
Para ello, realizamos test y pruebas de ensayo periódicas a todos nuestros materiales, así como controles de calidad para todos los procesos constructivos.
Los métodos de trabajo de nuestros operarios en las obras se ajustan a los requerimientos técnicos exigidos para reformas, según las normas técnicas correspondientes. Así como el utillaje y maquinaria utilizados tanto en la aplicación, distribución y fabricación.
Somos una empresa enfocada al trato personalizado con el cliente y por ello, IngreMic garantiza una hoja de ruta trasparente durante todo el proceso de ejecución de su proyecto.
Nuestros Showrooms y Fábricas reúnen todas las condiciones necesarias para ofrecer una atención personalizada y en circunstancias óptimas de servicio, ofreciendo la máxima comodidad y seguridad. Contamos con un excelente equipo técnico expertos en revestimientos continuos decorativos, que está a su disposición para asesorarle sobre cualquier propuesta o duda.
Estas instrucciones corresponden al estado actual de nuestros conocimientos y facilitan información general acerca de nuestros productos y nuestra empresa.
Alta resistencia
Especialmente diseñado para renovación de naves industriales, garajes de tráfico mecánico pesado e intenso, impidiendo la abrasión, en instalaciones como fábricas, áreas de producción y almacén. Altamente conveniente para ser revestido con pinturas epoxi, poliuretanos, linóleos, PVC, moquetas, parquet… Debiendo ser utilizado exclusivamente en interiores.
Nuestra carta de colores
-
microcemento ingremic color acero
-
microcemento ingremic color agreste
-
microcemento ingremic color amarillo polen
-
microcemento ingremic color amatista
-
microcemento ingremic color atracita
-
microcemento ingremic color arena
-
microcemento ingremic color arena caribe
-
microcemento ingremic color avellana
-
microcemento ingremic color azul cielo
-
microcemento ingremic color azul leal
-
microcemento ingremic color azul noche
-
microcemento ingremic color berengena
-
microcemento ingremic color blanco
-
microcemento ingremic color blanco fijo
-
microcemento ingremic color blanco niebla
-
microcemento ingremic color blanco roto
-
microcemento ingremic color blanco titanio
-
microcemento ingremic color chocolate
-
microcemento ingremic color ciruelo
-
microcemento ingremic color coco
-
microcemento ingremic gris
-
microcemento ingremic color gris acero
-
microcemento ingremic color gris cemento
-
microcemento ingremic color gris naval
-
microcemento ingremic color gris plomo
-
microcemento ingremic color gris tempestad
-
microcemento ingremic color gris topo
-
microcemento ingremic color gris versatil
-
microcemento ingremic color jotun piedra coral
-
microcemento ingremic color kenia
-
microcemento ingremic color malva
-
microcemento ingremic color mantecado
-
microcemento ingremic color marfil
-
microcemento ingremic color negro
-
microcemento ingremic color ocre
-
microcemento ingremic color perla
-
microcemento ingremic color perla paris
-
microcemento ingremic color plata
-
microcemento ingremic color purpura
-
microcemento ingremic color rojo ferrari
-
microcemento ingremic color rojo maya
-
microcemento ingremic color rosa natural
-
microcemento ingremic color sabia
-
microcemento ingremic color sahara
-
microcemento ingremic color sauce
-
microcemento ingremic color tejano
-
microcemento ingremic color terracota
-
microcemento ingremic color topacio
-
microcemento ingremic color tostado
-
microcemento ingremic color trigo
-
microcemento ingremic color verde alpe
-
microcemento ingremic color verde kaki
-
microcemento ingremic color verde pistacho
-
microcemento ingremic color verde sauce
-
microciment ingremic dry green color